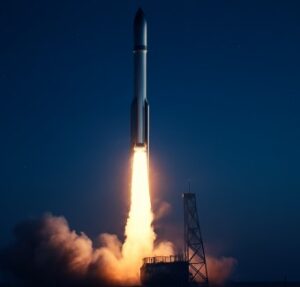
Before a payload or spacecraft reaches orbit, it must prove its reliability, resilience, and operational functionality under flight conditions. Suborbital testing offers a vital bridge between ground-based experimentation and the high-stakes environment of orbital missions.
Unlike laboratory simulations, suborbital flights expose systems to real-world dynamic stresses, including atmospheric ascent, thermal transitions, and high-G events. By validating components and subsystems early, developers can detect design flaws, refine integration strategies, and gather essential performance data—all at a fraction of the cost and lead time associated with full orbital launches.
Case studies across the aerospace sector highlight common failure points that could have been identified during suborbital testing: thermal protection degradation, electronic component malfunction under vibration, or mechanical misalignment under sustained G-forces. Suborbital platforms allow engineers to encounter and resolve these issues in a controlled, recoverable environment.
Moreover, pre-orbital testing is increasingly recognized within certification pathways, enabling companies to achieve Technology Readiness Level (TRL) milestones faster and with greater confidence. For emerging technologies, gaining flight heritage through suborbital missions significantly de-risks later orbital deployment and enhances investor and customer trust.
At IpaziaSpace, our suborbital launch services are specifically designed to support early validation and qualification efforts, offering flexible mission profiles, optional payload recovery, and rapid turnaround times. We provide a pragmatic path from prototype to proven technology—helping innovators move from concept to orbit-ready, reliably and efficiently.